Volumetric 3D-Printing builds parts in a single step, opens the door to faster, more diverse additive manufacturing
Collaboration between researchers at UC Berkeley & Lawrence Livermore National Lab leverages CT scanning concepts to build higher-performance objects in seconds.
Conventional Digital Light Processing (DLP) and stereolithography (SLA) additive manufacturing technologies have revolutionized the creation of custom, on-demand parts for a wide range of industries, most notably in the dental and medical industries. But even as these layer-by-layer 3D-printing technologies address an expanding range of markets, several limiting factors remain to be addressed—namely speed, mechanical performance and material limitations.
Now, a new 3D printing paradigm, Volumetric 3D printing, aims at overcoming these limitations and can instantly form a complete part in seconds by applying light energy into a rotating vat of photosensitive resin.
It may seem a bit like science fiction, but if researchers from Lawrence Livermore National Laboratory and the University of California, Berkeley have their way, that futuristic experience isn’t too far off. Thanks to a partnership between the two organizations, a high-speed volumetric 3D printing technique, called Computed Axial Lithography(CAL), can now build high-precision parts in a matter of seconds, opening the door to much faster, scalable additive manufacturing, from a wider range of materials, particularly in the biofabrication/bioengineering space.
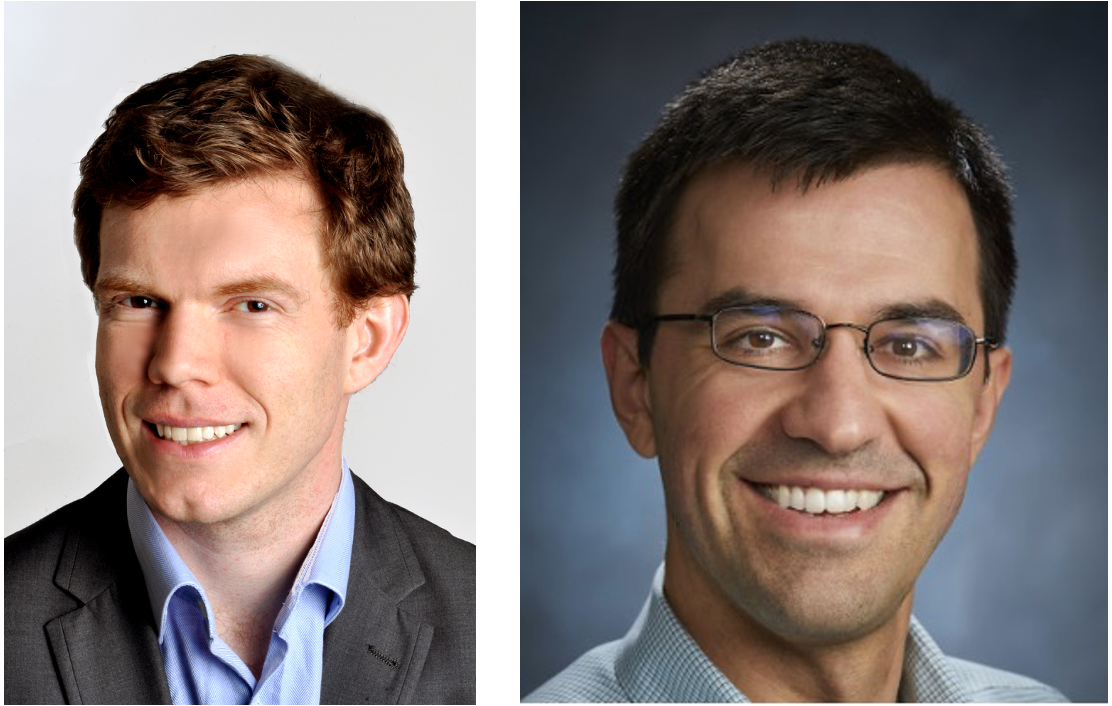
All-at-once vs. layer-by-layer
“Layer-based printing methods are limited in their speed by the hydrodynamic stresses that develop in the fluid—the light-sensitive precursor resin material—as the component being printed is drawn through a tray or bath of that material,” says Hayden Taylor, associate professor of mechanical engineering at UC-Berkeley. This process can take hours or even days depending on the size of the part being produced.
“In CAL, the object being printed does not move relative to the precursor resin during exposure, so the printing rate is limited only by the delivery of light dose and the ensuing polymerization reaction. This key difference means that a wider range of materials can be processed by CAL, including extremely high-viscosity or even solid, gelled precursors and those with a high loading of solid particles. Ultimately, we aim to bring CAL to a point where it can compete with injection molding for some applications.”
In addition to speed challenges, Taylor and his research partner, LLNL materials engineer Maxim Shusteff, say mechanical challenges also exist. Parts built layer-by-layer often result in a poor surface finish, which requires significant post-production surface treatment, and they could contain inherent stresses or flaws by nature of the layering process. Furthermore, conventional DLP-printed parts are built from the same material throughout, providing no easy way to combine different materials or insert a component within the structure.
The CAL approach seeks to address those problems by curing the material to form the entire part simultaneously, producing a smoother surface finish. The technique also enables the insertion of a different material—a metallic component, for example—within the vat of resin around which the printed part forms.
Taylor says the agility of the CAL system also enables the use of more delicate materials, like those used as scaffolds for engineered tissues in biofabrication applications. These are typically flexible and compliant, such as water-laden hydrogels, and the softest of them might otherwise be damaged during conventional 3D printing processes.
More recently, the team has also experimented with other types of resin materials, such as silicones, to expand the use of volumetric 3D printing into a wider range of applications.
Making CAL work
In order to achieve these milestones, the team has leveraged concepts from CT scanning, but in reverse. Whereas CT scanning acquires a series of 2D X-ray images from different angles, called projections, to reconstruct a 3D volume, the CAL technique works backwards, calculating the 2D projections needed to create the precise 3D distribution of energy to create the part. These projections are then directed into vat of resin. As the vat rotates, the projections overlap to form the part geometry. As the energy is deposited, the part solidifies within the resin bath, after which the excess uncured resin is drained away.
“We had to look at the curing process in much greater detail than in previous literature in order to understand the resin curing behavior at every point in space—and be able to control it.”
Maxim Shusteff, Materials Engineer at Lawrence Livermore National Lab
Of course, working in three dimensions introduced several challenges. First, the computations that generate the projections involved need to account for all the relevant variables: light distribution, the performance of the optics, the photochemical response of the resin and its dynamic curing behavior, to name a few. The team also had to figure out how to deliver the energy needed throughout the resin to achieve simultaneous curing without overheating it and causing auto-acceleration, a phenomenon in which the heat produced by the chemical reaction causes additional, unintended reactions.
“At one point in our experiment, the material actually began smoking as it heated up well beyond 100 degrees Celsius,” Shusteff said. “We had to look at the curing process in much greater detail than in previous literature in order to understand the resin curing behavior at every point in space—and be able to control it.”
“The project requires a variety of expertise in chemistry, computational mechanics, optics, and other fields,” he said, noting that several talented and enterprising grad students have been involved in the research over the last three years. “That’s one great thing about working with Livermore—they have a wide range of expertise on staff and that really accelerates the technical growth of the Berkeley graduate students who are developing CAL as part of their PhD research.”
“The CAL concept is clearly catching on across the academic world, and the potential impact, particularly in biofabrication, is very exciting, but there are still some hurdles to overcome. I hope that with global collaboration, we’ll soon see this technique deployed on a commercial scale.”
Hayden Taylor, associate professor of mechanical engineering at UC-Berkeley
The Future of CAL-based Additive Manufacturing
As the CAL team looks ahead to a multitude of applications for their technique, Taylor says finding available projection light engines could be a challenge. Because most LED hardware is optimized for video projection and the DLP layering approach, the team has had to be a bit creative.
“We need a different focal configuration from layer-based processes: one that has a relatively large focal depth,” he says. “As we move to larger printing volumes, we also need to consider how the optical system can access the full printing volume without becoming unwieldy. And we will likely need more power from illumination systems to maintain high volumetric processing rates at larger volumes.”
Meanwhile, the CAL team’s work is gaining worldwide momentum. A number of research projects building off their foundation have emerged at the Centre for Additive Manufacturing at the University of Nottingham, the Zhang Lab for Engineered Living Systems at Harvard University, the University of Nebraska’s Mechanical & Materials Engineeringdepartment, in Mainz, Germany and other parts of Europe.
“The CAL concept is clearly catching on across the academic world, and the potential impact, particularly in biofabrication, is very exciting, but there are still some hurdles to overcome,” Taylor said. “I hope that with global collaboration, we’ll soon see this technique deployed on a commercial scale.”