From one to multi materials
Ph.D. candidate at McGill University Vahid Karamzadeh told us about how multi-material DLP 3D-printing can bring us closer to 3D printing functional tissues.
3D printing has seen enormous growth and advancement in just a few decades, from the complex structures, innovative materials, and even printing methods. One such advancement is multi-material 3D printing, when the structure is created from two or more different materials at the same time.
In true multi-material extrusion printing, materials are swapped out so quickly and automatically that they do not disrupt the build or multiple nozzles with different materials in each can be used simultaneously. There is another approach, through DLP, however, which is more accurate and does away with the danger of accidentally mixing materials through inaccurate nozzles. The light-waves from the light projectors control how each material is formed and cured, and this newer approach -- while still in early development stages -- shows amazing promise for all industries. This is especially true for biotech.
Common bioprinting obstacles
The field of bioprinting has changed dramatically over the past few years. What once consisted of 3D printing separate scaffolding structures compatible with living human cells has now evolved to include cells within the printed material that crosslink when exposed to light. Because printing structures as delicate as cell material has risks, the technology needed to ensure cell viability and integrity must be precise and provide an environment that biomaterials can survive in for the duration of the build.
There is also the challenge of 3D printing biomaterials containing human cells, which are "multicellular constructs with hierarchical structures.” One way to get the best result possible is with multi-materials 3D printing. For the biomaterial field, this may mean 3D printing structures made from one type of cell-laden ink, then switching mid-build to another.
We spoke with Vahid Karamzadeh, Ph.D. candidate at McGill University who previously worked at the Organ Manufacturing Group at United Therapeutics Corporation about what challenges currently exist for this technology and what the future holds for reproducing complex organs, like a lung or kidney, especially as multi-material technology gains traction.
“You can achieve higher resolution compared to other methods, such as extrusion-based bioprinting, and the throughput is much higher”
Vahid Karamzadeh about multi-material 3D printing
Multi-Materials: New opportunities in bioprinting
It once was possible to only print less complicated organs, such as skin or cartilage, since these had a relatively consistent structure with less complex cellular makeups. Karamzadeh reveals that, while printing complex organs with intricate vascular systems and thousands of tiny capillaries is a way off, progress is being made.
These 3D-bioprinted organs, which could be instrumental in drug discovery and testing, must be carefully and quickly assembled. They must also be made from a variety of bioinks at once – not the single material commonly used in broader DLP vat photopolymerization applications.
Karamzadeh has spent his time researching photopolymerization methods for multi-material 3D printing and he shares the main advantages of using it as a platform for biofabrication:
“You can achieve higher resolution compared to other methods, such as extrusion-based bioprinting, and the throughput is much higher,” he says. “The printing speed is higher, so you can print a larger scaffold within a shortened time. And that's very important for bioprinting because you don't want to have cells outside of suitable environment for a long time.”
When compared to extrusion, inkjet, and LIFT, vat photopolymerization outweighs the rest in terms of ease of use, resolution, printing speed, overall build volume, and potential to handle the vasculature of more complicated organs. So, why isn’t it already being used for multi-material applications in the biotech industry?
Karamzadeh admits that the main challenge with multi-material methods, which require the polymer to be switched out in a complicated material exchange where the chance of contamination or even dehydration is higher. While this material swap still has merit, additional steps should be taken to reduce the corruption of the materials when using photopolymerization methods and to realize the full benefits of DLP 3D printing for multi-material applications.”
Some examples of 3D bioprinted materials in Vahid Karamzadeh's lab:
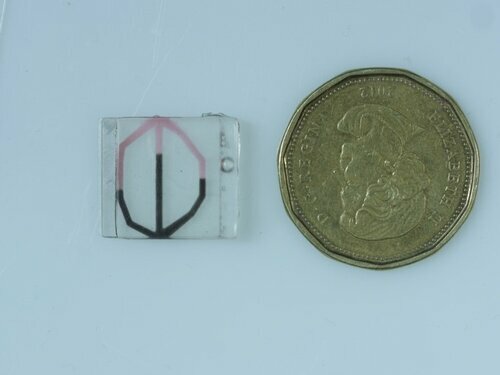

"The 3D bioprinting market is expected to reach USD 2398.27 million by 2026 which shows it is a fast-growing market.”
Previously, multi-material technologies were mostly limited to biomedical engineering labs with essential engineering backgrounds for its development. Most commercial bioprinters are based on the extrusion technique due to its accessibility, affordability, and easy-to-use platform. There is still an unmet need for commercial multi-material
vat-photopolymerization bioprinters to make these technologies accessible and available to more research labs and industries, where they can be used for cutting-edge applications.
Using a DLP 3D printer, you can 3D assemble and pattern multiple cells and biomaterials to recapitulate the intrinsic microarchitectural organization of native tissues. However, further improvement is needed in the rapid bioink-exchange process with minimal bioink cross-contamination and high cleaning efficiency. Pharmaceutical companies such as United Therapeutics has already applied light-based 3D printing for the manufacturing of human organs. The 3D bioprinting market is expected to reach USD 2398.27 million by 2026 which shows it is a fast-growing market.”
Why projection systems matter in multi-materials?
Despite all the promise of what could be with multi-materials, the basic technology that makes DLP printing work so well should be understood better to ensure the best results in a mult-material setting.
Digital light projectors offer flexibility and strength. They are already being used in various applications, including multi-material bioprinting at both the academic and commercial levels.
How does this apply to the concept of multi-material printing? Karamzadeh sees multiwavelength approach as a way to use two different projectors with two different wavelengths within the same setup. This newer approach is still in development but could offer scientists more flexibility in multi-material 3D printing applications. Trials have been done with non-living materials and UV DLP printing light sources, where multiple lights were shown into the vat to create varying reactions and different properties in the final structure. As more research is done on what happens when more than one light source is used at once, this method could also take its place in the tissue engineering realm by using biocompatible inks.
He also referred the reader for more information about multimaterial 3D bioprinting to his recently published paper in the journal of Advanced Materials titled “Emerging Technologies in Multi-Material Bioprinting”.