Beyond Polymers
A review of the wide range of materials available for DLP 3D-printing, from ceramics to nanocomposites.
DLP 3D-printing has many benefits. Among them is versatility, since the process can turn any number of photopolymers from a liquid resin to a solid structure of intricate design. It’s notable for its high resolution and the speed of output. While it was initially used with photopolymer resins consisting of monomer and oligomers in liquid state combined with a photoinitiator, the range of materials has grown. Developers are constantly working to extend the range of physical and chemical properties of the materials available for DLP 3D printing.
What are the top materials to use? While your choice will depend on the results you hope to achieve, ceramics, metals, and polymer-composites are the most recognized categories of materials used for DLP today. With these new materials at their disposal, designers and engineers can leverage the speed and high resolution of DLP 3D-printing for a wider range of applications. We’ll go through these materials and applications below.
How materials are used in DLP
Ceramics and metals can be added in powder form to the photopolymer resin to form a slurry. Some of the slurries on the market are pre-mixed for easier handling, such as those marketed directly to consumers. This slurry is the material that fills the vat of the 3D printer, awaiting the photoreactive process that happens when it’s hit by the UV LED light. Each layer is flashed by this light; then it takes form as it cures. In this case, the polymer acts as a binder in the forming process of the final object and is removed afterwards. The object formed through the photopolymerization process is called the “green part”. It contains ceramics or metal particles densely bound together in a polymer matrix. The green part is delicate and has to go through a debounding process to remove the polymer binder, and a last sintering step to achieve the final hardness and physical properties desired by the manufacturer.
In the case of polymer composites, a material is added to the polymer resin in order to give it additional strength, conductivity, etc.
Ceramics
The benefits of ceramics are many. When cured by the DLP light source, a very fine surface texture can be achieved, which is why those looking for complex geometries often turn to ceramics for their builds.
Within the ceramic category, there are several materials that offer a wide range of properties and best uses.
They include:
- Al2O3 (Alumina)- Alumina is known to be hard, nonconductive, very stable in extreme temperatures, and greatly resistant to wear, it is found in medical implants, semiconductors, insulators, and water purification parts.
- Hydroxyapatite – Inside your bones and teeth is a material known as Hydroxyapatite, and it’s being used to print implants that mimic the way natural body parts function. Its porous nature makes it incredibly biocompatible, yet it’s strong enough to stand in for bones in the skull, limbs, and even the spine. Because it’s a natural material, it is praised for its osseointegration possibilities.
- SiO2 (Silica) – Most notable in the aerospace industry, this material offers thermal shock resistance that’s superior to most other 3D printed materials. It’s currently used for casting parts.
- ZrO2 (Zirconia) – A biocompatible material that stands out with natural beauty, it’s a fine pick for jewelry, in addition to dental components, bearing, and extrusion dies. Its low thermal conductivity, fracture resistance, and toughness ensure it can be used for parts that need to last a long time.
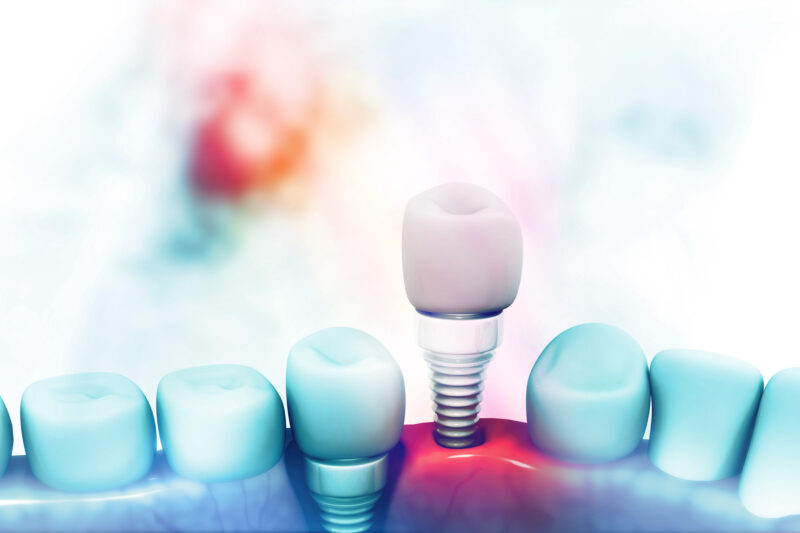
Metals
Metal casting can be expensive, and C&C machines are impractical for many applications where a smaller print bed or less waste is ideal. Photopolymers mixed with a metal powder can achieve the look, feel, and strength of traditional metal casting, but with more flexibility and detail.
Consider these DLP print options if shine, sturdiness, and resistance to rust or corrosion are your aim. Since the metals can be ground down into fine powders and combined in a homogenous manner with the liquid resins, they produce consistent outcomes with the physical properties of the original metal.
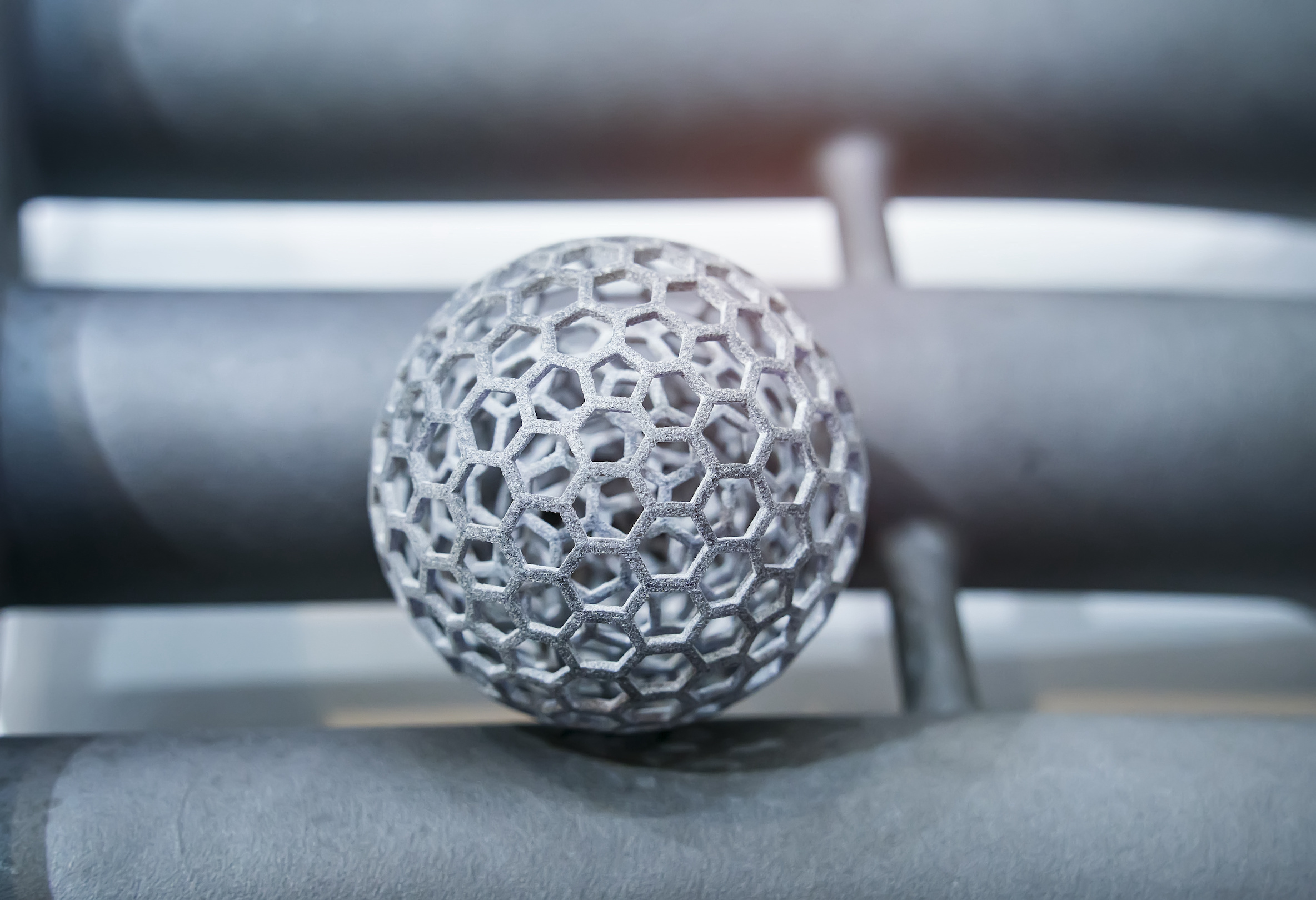
- Copper - Copper is among the softest metals, and it is a good match for DLP printing applications. As one of the best thermal and electrical conductors, it’s frequently used to print heat transfer and induction coil parts. Its resistance to humidity makes it an HVAC favorite. You may also find it in radio frequency Cathodes, which are increasingly being made with 3D technologies.
Companies are already making “cool plates” for computers using copper photopolymers. These structures carry heat away from chips and other heat-prone parts. 3D printing is one of the only ways to create such a delicate and intricate design using copper.
- Inconel 625 – This alloy mixture combines chromium, nickel, and molybdenum to make a heat and oxidation resistant material that’s ideal for aerospace and automotive functions. As it holds up well to chloride ions, it’s often used for parts that need to hold up well in ocean water.
- Stainless steel – Not all stainless is the same, with the more common types being 316L, 304, and 17-4. 316L is highly resistant to corrosion, non-magnetizable, and easily weldable; it is ideal for medical devices, food processing equipment, and decorations. Stainless steel 17-4, on the other hand, is a more well-rounded metal for the cost. It is ideal for those hoping to simplify manufacturing without sacrificing hardness, strength, or corrosion resistance. You’ll find it in automotive, aviation, and boat parts.
Polymer-based composites
Polymer composites are a recent addition to the DLP material family and open the door to new applications where stronger, lighter or more conductive materials are required. Research and development will continue to bring about exciting polymer blends. Here are a few to keep an eye on:
- Carbon fiber: A newer addition to the photopolymer family, carbon fiber has many possibilities. Carbon fiber has been used since the 70s for automotive manufacturing, planes, and any other uses where parts needed to be as light as possible without losing strength, as well as in everyday objects like tennis rackets and bike frames. 3D printing with this material has been limited until just recently to extrusion printing methods, but some new developments promise to do more than ever before.
One example is the use of magnets to align particles in the carbon fiber materials to make them sturdier than if they weren’t aligned. (Much like how wood fiber strength comes from the consistency of the grain, this carbon fiber alignment helps reinforce the build structure.) After the resin slurry is subjected to a magnetic field and the alignment is achieved, it is then hardened using UV light, just like in traditional DLP printing.
Expect the carbon fiber options to grow over time, as many more manufacturers look for a way to use this incredibly durable and versatile material in all print processes.
Some interesting research is being done aiming at integrating nanoparticles into photopolymer resins in order to achieve higher conductivity or strength, for example:
- Carbon nanotubes: These materials are already used in a wide range of applications for their mechanical, electrical and thermal properties. Researchers are working on ways to add them to photopolymer resins and leverage the high resolution and speed of DLP 3D-printing to create complex structures with electrical properties. This could lead to new ways to manufacture electronic components.
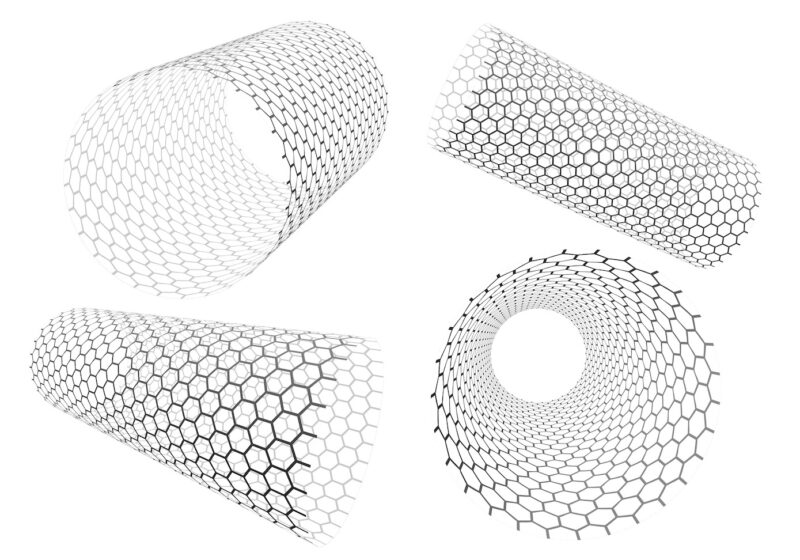
- Silver-nanowire (Ag-NW) composites could possibly be used for scalable processes that require high conductivity. Examples of future products include biosensors, touchscreens and flexible electronics.
- Graphene-reinforced nanocomposites (GNPs) may someday be used for tissue engineering or personalized medical devices that require complex structures at a lower cost.
Adding nanoparticles to the resin tend to interfere with the photopolymerization process, hereby leading to partially cured areas in the print. This could be overcome with higher light intensities like the one offered by the Helios light engine.
New developments in material science are going to keep enabling exciting applications with DLP 3D printing. As these new materials enter the market, the need for a quality DLP printer - and a UV DLP projector that can provide the right amount of light and the high resolution - will grow.