4DbloodROT - Heart Pump Rotor from the 3D Printer
Novel rotors for heart pumps have been developed in collaboration with the research companies Joanneum Research and Polymer Competence Center Leoben GmbH, the Montanuniversität Leoben and Lithoz GmbH.
In the course of a research project, In-Vision has participated in the development of novel rotors for heart pumps in collaboration with the research companies Joanneum Research and Polymer Competence Center Leoben GmbH, the Montanuniversität Leoben and Lithoz GmbH. These new types of rotors can be manufactured much faster and more precisely than the solutions used previously. The insights gained have raised the potential for the volume (metric) production of polymeric parts using 3D printing to a new level.
Around one third of all people over the age of 55 suffer from cardiac insufficiency which is an acutely life-threatening condition, with five-year survival rates worse than most cancer types. Heart transplantation is considered the gold standard in the treatment of severe heart failure. However, treatment often fails because only a fraction of patients receive suitable donor hearts.
Even those patients who are most in need have to expect long waiting times. Heart pumps, which are inserted directly into the veins, are an important tool to bridge the time to surgery and increase survival. But even patients whose heart failure is treated with medication often need a heart pump to support them, at least for a while.
Biocompatible material
Manufacturing of such pumps is a major technical challenge. The complex rotor geometry in particular must be hydrodynamically and mechanically optimized, which presents difficulties. At the same time, the material used must remain in the body for as long as necessary without causing side effects.
Titanium, which is used for conventional heart pump rotors, partly meets these requirements, but it also has disadvantages: Conventional machining processes cause problems in manufacturing very complex and precise heart pump rotors. However, the surface of a rotor made from such a material would have to be designed to prevent platelets from adhering. If platelets adhere to the rotor and clump together, there is an acute risk of cardiac thrombosis and thus of death. This is another point that has repeatedly caused concern with conventional titanium rotors.
Better blood compatibility
In a joint project with the research companies Joanneum Research and Polymer Competence Center Leoben GmbH, the Montanuniversität Leoben and Lithoz, In-Vision has therefore collaborated on the development of a new rotor that can solve many of the previous problems. The name of the project, 4DbloodROT, refers to the goals that have been set: To design a rotor (that's what the English word ROT stands for) that can be used in a blood pump (that's what blood stands for) and that can be manufactured using 3D printing. The name 4dBloodRed refers to the fourth component besides three-dimensionality - namely, the biocompatibility of the material.
"The goal of the project was to find a surface design that would allow us to make a heart pump rotor out of biocompatible resin using DLP printing. The advantages of such a process are clear. With DLP printing, for complex parts you can achieve an accuracy and also a manufacturing speed that is not possible in this form with classical processes," says the project's technical and operational supervisor Reinhard Kaindl of Joanneum Research.
Project manager Jürgen Lackner brings other advantages into play: "DLP printing also allows for greater flexibility in geometry. The synthetic resin used also offers very good blood compatibility."
Two Firebird modules and a new lens
The printer used in the project was designed and built by Lithoz, and In-Vision developed the light engine used within. "The big challenge," says Wiebke Jahr, who oversees the project at In-Vision, "was to achieve the resolution that would meet the very high accuracy demands of a blood pump rotor. After all, it really can be a matter of life or death here."
The solution the project team chose was to stitch two Firebird platforms together, nearly doubling the usable area. This allowed them to expose an area twice as large while maintaining the same level of precision.
However, the development of the system was anything but trivial. A way had to be found to minimize distortions and aberrations even at the edges, which inevitably come to rest centrally when two light engines are joined together. To reach this goal, In-Vision worked with Lithoz to develop an optical system in which the light does not come directly from below, but instead is deflected. For the future, this process can open up a whole range of new possibilities, even beside heart pump production, because it significantly expands the space that can now be printed with the utmost precision.
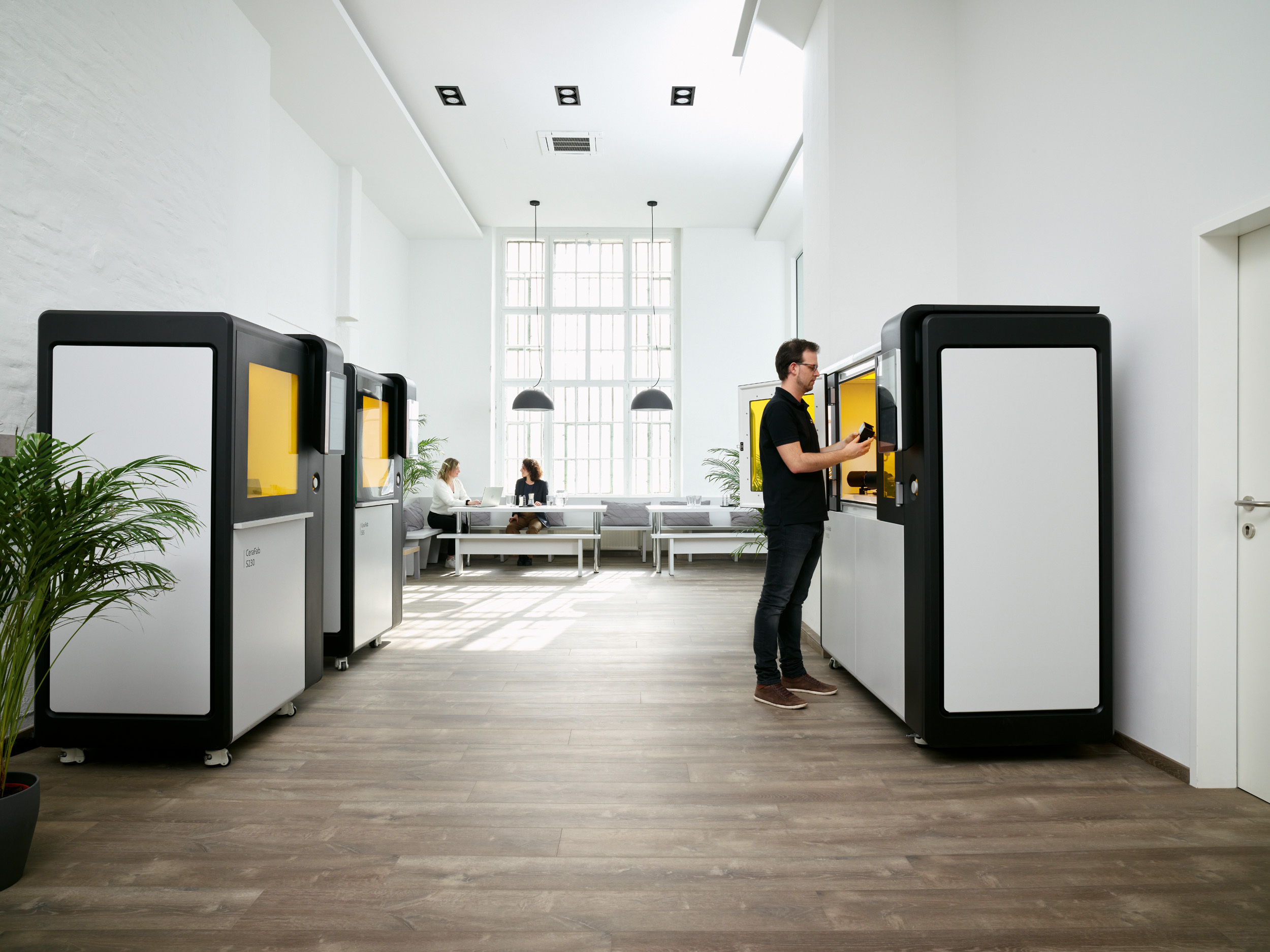
Norbert Gall, head of marketing at Lithoz GmbH, cannot reveal anything concrete about customers who want to use the new system in the future for reasons of confidentiality, but he assesses the potential of the development very positively not only for polymers but also for the printing of ceramics: "Such ceramics play out their strengths above all in precision, surface quality and the quality as well as homogeneity of the achievable component properties," he explains. Accordingly, 3D printing of ceramic parts using LCM (lithography-based ceramic manufacturing) technology is now also the global industry standard. "The added value from the 4DBloodRot for Lithoz GmbH is particularly the higher intensity at the same resolution and build field size. This really opens up the market for materials that are more difficult to process.
More about 3d printed medical solutions
In-Vision's newsblog offers more interesting articles about 3d printed medical solutions like:
- Interview with bioprinting pioneer Prof. Dr. Y. Shrike Zhang from Harvard University answering the myth: "When will the first organ come out of the printer?"
- Prof. Dr. Jürgen Stampfl form Vienna University of Technology talking about "Design for Disassembly" in the dental sector
- 3D-Printed Microneedles for Continuous Glucose Monitoring
- Advancing Soft Tissue Regeneration with DLP 3D Bioprinting
- An Austrian startup has found a way to make orthotics more comfortable
Rainhard Kaindl
Technical and operational supervisor of the project
Joanneum Research
Jürgen Lackner
Project Manager
Joanneum Research